PORE-FLO: Porous material that produces excellent rectification effects
PORE-FLO is a multifunctional porous material consisting of two or three layers of flat woven wire mesh, sintered, and rolled into one. Each PORE-FLO panel has uniformly sized pores ranging from tens of microns to approximately 100 microns, with an even pressure drop distribution. It is utilized in areas where rectification, powder conveying, diffusion, drying and cooling, infiltration, and resistive elements are required.
The standard material is 316L stainless steel, which has excellent mechanical strength, heat resistance, and corrosion resistance.
Main Applications
Other
Purpose/Use
- Rectification
- Powder treatment (air supply, degassing)
- Powder treatment (cross-linking prevention)
Product Features
Uniformity
There is little variation in pressure drop and even gas dispersion.
Rectification
Minimizes ever-changing air velocity fluctuations.
Discharge
The residual volume of powder at the time of discharge can be minimized.
Flowability
Can flow at a gradient of less than the angle of repose (can also flow at a reverse gradient, depending on the powder).
Composition of PORE-FLO
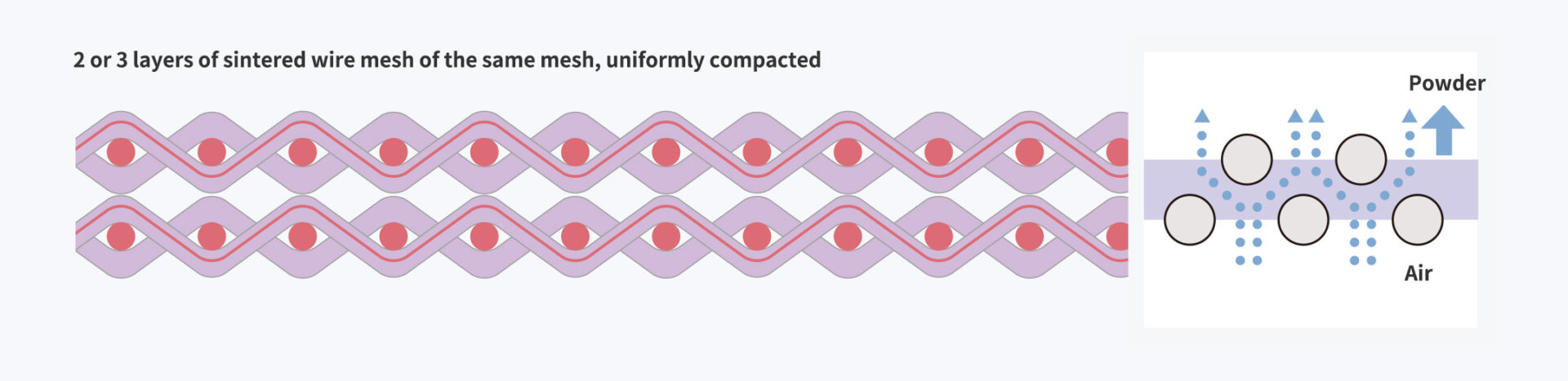
Specifications
As standard, 8 types of 2-layer (D-type) and 8 types of 3-layer (T-type) flow rate to pressure drop characteristic panels are available.
Material
The standard material is 316L stainless steel. Other special materials can be adapted, so please consult us for details.
Processing
With a strength of 100 to 150 N/mm2 in expansion force and 15 to 25% in elongation, it can be used for cutting, drilling, punching, and drawing processes. It can also be used for welding processes such as TIG and plasma welding.
Standard Filtration Configuration
Model No. | Standard wire mesh configuration (mesh) |
---|---|
P2 | 100+325/2400+100+12/64+64/12 |
P5 | 100+200/1400+100+12/64+64/12 |
P10 | 100+165/1400+100+12/64+64/12 |
P20 | 100+165/800+100+12/64+64/12 |
P40 | 100+50/250+100+12/64+64/12 |
P75 | 100+200+100+12/64+64/12 |
P100 | 100+150+100+12/64+64/12 |
P150 | 50+100+40+20+40+100+50 |
P200 | 50+80+40+30+40+80+50 |
Dimensions
- Standard size (panel size when sintered) 500 x 1000 mm
- Standard sheet thickness D type…0.7 to 1.3t T type…1.5 to 2.0t
- Various sizes of cylinders, cones, discs, square plates, etc. can be processed from these sheets.
- Flanges, reinforcements, mounting frames, and other fittings can also be welded.
Flow characteristics (Fluid name: air)
*We can also manufacture flow rate characteristics other than those listed above. Please contact us.
Example of PORE-FLO use
Purpose/Use
Industry
Disc filter
- Rectification
- Powder treatment (air supply/degassing)
- Food and beverage industry
- Pharmaceutical and cosmetic industry
- Chemical industry
Conical filter
- Rectification
- Powder treatment (air supply/degassing)
- Food and beverage industry
- Pharmaceutical and cosmetic industry
- Chemical industry
Poppers for powder equipment
- Rectification
- Powder treatment (cross-linking prevention)
- Food and beverage industry
- Pharmaceutical and cosmetic industry
- Chemical industry
Air roll
- Rectification
- Pharmaceutical and cosmetic industry
- Chemical industry
- Plastic, fiber and film industry
- Precision machine parts
Custom-ordered products
For special applications such as high temperature and corrosion resistance, we can design and manufacture “custom-made” products that meet your specifications. Please contact us.
Cleaning Methods
Appropriate cleaning methods (reverse filtration, solvents, ultrasonic cleaning) enable perfect regeneration.
Reference
Selection Method
- Purpose (powder conveying, bridge breaker, chemical treatment, aeration, etc.)
- Shape and mounting structure
- Air (or other gas) flow rate and pressure drop
- Powder properties (type, particle size, shape, density, bulk density, angle of repose, etc.)
- Powder throughput
- Supplied air conditions (blower, compressor, pressure, etc.)
- Design conditions (temperature, pressure, pressure resistance, material, etc.)
Cleanliness of supplied gas
Clean gas should be supplied to the PORE-FLO. As a rule of thumb, use “instrument air” or remove dust and oil mist of 5 µm or more.